Lean manufacturing, also known as lean production or simply lean, has emerged in response to the challenges faced by companies over the last decade. It is a system of production that encourages companies to eliminate wasteful practices through continuous improvement, so they can dramatically reduce lead times and cut down on defects.
Lean manufacturing is not just a set of tools and methods but also a way of thinking and looking at a business from both inside and outside. As such, it lies at the heart of new approaches to management, marketing, design, engineering, logistics, and supply chain management.
This article will explore what it means to be lean then look at six ways every company can develop an effective lean manufacturing process:
1. Actively Look For Waste
Manufacturing processes are often wasteful, but where there is waste involved, there is an opportunity for improvement that can save money and time; therefore, it is important to be aware of these situations as they arise.
Employees may lack the necessary skills or tools (or training on them) to do their jobs properly or sufficiently—which often leads to inefficiencies. The development of a lean culture within an organization is key when it comes to recognizing and eliminating these wastes in your processes.
2. Focus on Customers
To focus on eliminating waste from the process, you need to know what your customers want from their interactions with your business. Every interaction with a customer could be seen as a “transaction,” but not every interaction with a customer is an equally valuable one.
Identifying the truly important transactions that drive value for customers and then focusing on those will lead you down the path of the least resistance when looking for ways to eliminate waste in your manufacturing process. You can get customer feedback by gathering data through questionnaires or other forms of inquiry without interrupting their workflow.
3. Be Proactive, Not Reactive
When problems arise in manufacturing, it is because someone was not thinking ahead—they failed to set standards or understand the process itself well enough—and now they are wasting time and money trying to fix it. Being proactive requires foresight; anticipating possible issues before they happen will help you eliminate waste before it becomes a bigger problem than anything else.
Do not be afraid of asking for help either; you can never know everything there is to know about every aspect of your business, so getting opinions from other people within the company on how best to handle certain situations will allow you to move on with more knowledge on why things might go wrong if you do not act proactively.
4. Measure What Matters
To improve your company’s processes, you need to know where there is room for improvement; measuring key metrics will allow you to do this and make informed decisions about how to progress forward.
The best way to measure what matters is by using small-scale projects that help employees identify opportunities for process improvement by making accurate measurements of the existing methodologies in place; these can be measured against established goals that act as benchmarks towards continuous improvement.
5. Use the Right Equipment
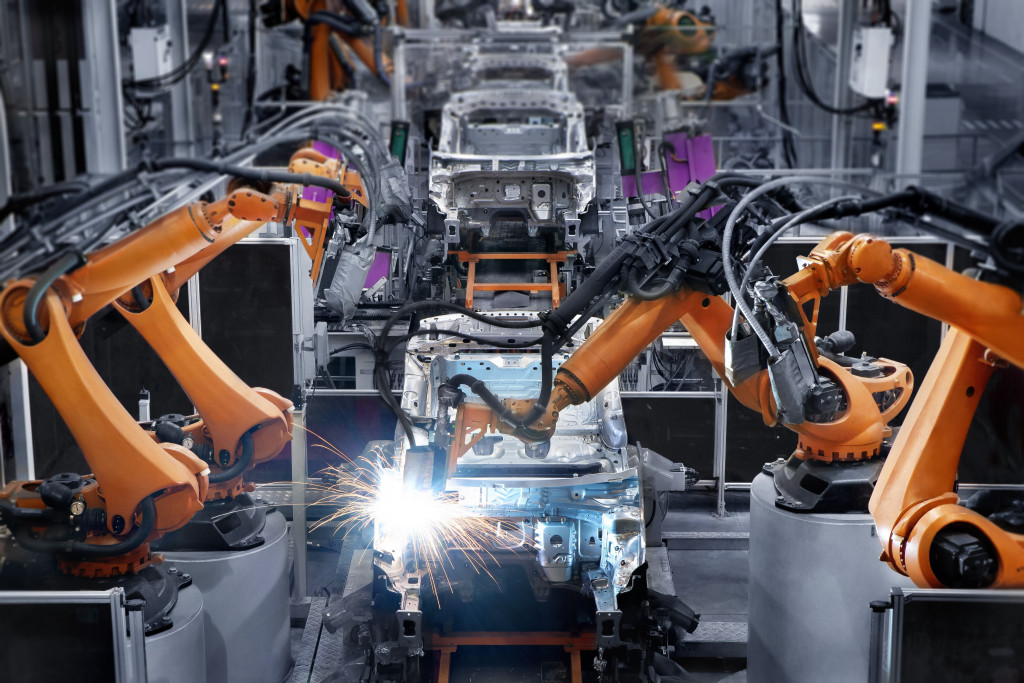
You cannot eliminate waste from your manufacturing process if you are using the wrong equipment for the task at hand. Before purchasing new equipment, make sure it is necessary and efficient. It should also be easy to use, clean, maintain and repair because workers will not be able to do their jobs properly if they have tools that are difficult or time-consuming to use—the job will simply take too long because of it.
Make sure everyone working with this equipment has been taught how to use it, so there is no delay in waiting for an expert to show them how it works either. Use equipment that streamlines the manufacturing process and saves time, money, and resources. For instance, electric actuators can be used to open and close valves on a production line while maintaining the same momentum every time. This will help optimize the manufacturing process.
6. Communicate Effectively with Stakeholders
People within an organization must be able to communicate effectively with one another if they want to make any headway towards eliminating waste from their manufacturing process—this means establishing a common vocabulary that allows them to talk about the process without ambiguity.
Employees need to be able to ask questions if they are unsure about anything but be prepared to provide answers clearly and efficiently, so there is no waste of time or resources. To create this common vocabulary, you need active listening skills—listen carefully and make sure everyone understands one another before moving forward.
By employing lean tactics in the workplace, you can reduce wasteful behavior and make better decisions about how to improve processes that are currently in place. The six strategies we’ve outlined above should help get you started thinking about how an efficient production process might look for your company!